jar546
CBO
So this method of construction confused me a little bit. I had to do a rough electric on a new Starbucks building, not a fit-out of existing. The interior slab was not poured yet yet the walls were framed inside the CMU. Since this is Florida and CMU exterior with tie-beams is standard, we normally only see the interior framed out after the slab is poured. In this case, the interior framed walls were essentially suspended over the dirt. There was very little electric, just a few boxes with conduit and no wire and nothing underground to look at. It gets better.
I'm told they needed the electric and framing inspection so they could install drywall and then they were done. Then a separate fit-out crew(contractors) comes in, rips the drywall off and does the fit out. This is one Starbucks, not to be separated into different tenant spaces. I never saw or heard of a process like this before.
Why not just do the underground, pour the slab and then frame? Weird.
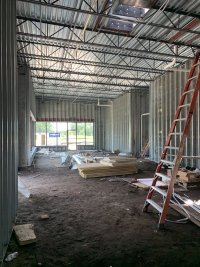
I'm told they needed the electric and framing inspection so they could install drywall and then they were done. Then a separate fit-out crew(contractors) comes in, rips the drywall off and does the fit out. This is one Starbucks, not to be separated into different tenant spaces. I never saw or heard of a process like this before.
Why not just do the underground, pour the slab and then frame? Weird.
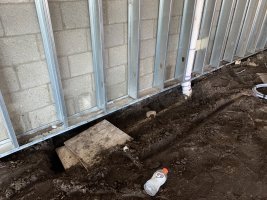
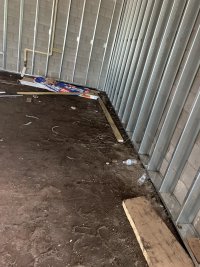
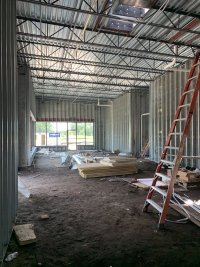