jar546
CBO
**NOTE - This is informational only since we have some difference of opinion as to what the purpose of plan review is and how far we are suppose to take it. Today I had one such example of why we need to be familiar with the basics to ensure the correct submission was made. Yes having an engineer or architect would be preferable but that is not always possible in 90+% of municipalities. Here we go.
I have a condo on a barrier island in a 170mph wind zone. The entire island has been deemed Exposure Category D. A new impact slider is being installed on the 5th floor of a 126' tall high-rise condo. The initial submission for wind pressures from the GC came from his PE and looked like this: (partial view)
Unfortunately he used the wrong Exposure Category of C and has the building height way, way off at 45'. This changes the pressures significantly, enough that it may require a different product to meet the positive and negative pressures. After rejecting this from the PE, he was thankful that the error was caught and resubmitted calculations that had at least the correct data. This is important to us because we now have in our possession the design requirements for this installation that shows the correct Wind, Exposure and Roof heights and the pressures are now more consistent with similar projects with similar sized sliders.
Here is the revised calculation (partial):
The design pressures need to be a minimum of +59.64psf and -75.39psf
Unfortunately the slider proposed has a maximum pressure rating of:
This is why I feel it is so important to verify as much as you can within the scope of your job. Around here it is expected that you do this at a minimum. Thoughts?
I have a condo on a barrier island in a 170mph wind zone. The entire island has been deemed Exposure Category D. A new impact slider is being installed on the 5th floor of a 126' tall high-rise condo. The initial submission for wind pressures from the GC came from his PE and looked like this: (partial view)
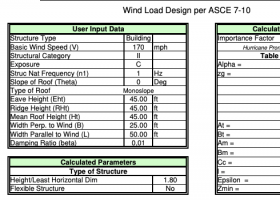
Unfortunately he used the wrong Exposure Category of C and has the building height way, way off at 45'. This changes the pressures significantly, enough that it may require a different product to meet the positive and negative pressures. After rejecting this from the PE, he was thankful that the error was caught and resubmitted calculations that had at least the correct data. This is important to us because we now have in our possession the design requirements for this installation that shows the correct Wind, Exposure and Roof heights and the pressures are now more consistent with similar projects with similar sized sliders.
Here is the revised calculation (partial):
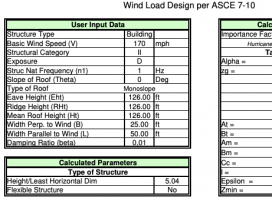
The design pressures need to be a minimum of +59.64psf and -75.39psf
Unfortunately the slider proposed has a maximum pressure rating of:
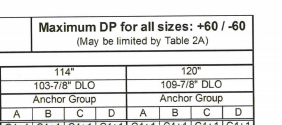
This is why I feel it is so important to verify as much as you can within the scope of your job. Around here it is expected that you do this at a minimum. Thoughts?