Hi, I'm not too familiar with the Ontario Building Code but I don't think this pvc pipe penetrating through a concrete fire separation is fireproof properly. It is in a residential condo. Can anyone with more experience with the code confirm? Thanks.
I found this in the code, but not sure if this is applicable to this situation:
3.1.9.4. Combustible Piping Penetrations
(1) Except as permitted by Sentences (3) to (8), combustiblepiping shall not be used if any part of the piping system penetrates,
(a) a fire separation required to have a fire-resistance rating, or
(b) a membrane that forms part of an assembly required to have a fire-resistance rating.
(2) Combustiblepiping that is part of a system described in Sentence (1) shall not be located in a vertical service space.
(3) Except as provided by Sentences (4) to (7), combustiblepiping is permitted to penetrate a fire separationrequired to have a fire-resistance rating or is permitted to penetrate a membrane that forms part of an assembly required to have a fire-resistance rating, provided the piping is sealed at the penetration by a fire stop that has an F rating not less than the fire-resistance ratingrequired for the fire separation when subjected to the fire test method in CAN/ulc-S115, "Fire Tests of Firestop Systems", with a pressure differential of 50 Pa between the exposed and unexposed sides, with the higher pressure on the exposed side.
(4) Except as required by Sentence (7), combustibledrain piping is permitted to penetrate a horizontal fire separation, provided it leads directly from a noncombustiblewater closet through a concrete floor slab and the piping is sealed at the penetration by a fire stop in conformance with Clause 3.1.9.1.(1)(a).
(5) Except as required by Sentence (7), combustiblepiping is permitted to penetrate a vertical or horizontal fire separation, provided the fire compartmentson each side of the fire separation are sprinklered and the piping is sealed at the penetration by a fire stop in conformance with Clause 3.1.9.1.(1)(a).
(6) Except as required by Sentence (7), combustiblepiping not more than 25 mm in diameter containing chlorine gas is permitted to penetrate a fire separation between a chlorine gas service room built in conjunction with a public pool or public spa and the remainder of the building, provided the piping is sealed at the penetration by a fire stop in conformance with Clause 3.1.9.1.(1)(a).
(7) Where combustible piping penetrates a firewall or a horizontal fire separation described in Sentence 3.2.1.2.(1), the piping shall be sealed at the penetration by a fire stop that has an FT rating not less than the fire-resistance ratingrequired for the firewall or horizontal fire separation when subjected to the fire test method in CAN/ulc-S115, "Fire Tests of Firestop Systems", and,
(a) the fire stopshall have been tested with a pressure differential of 50 Pa between the exposed and unexposed sides, with the higher pressure on the exposed side, or
(b) the fire compartments on each side of the firewall or horizontal fire separation shall be sprinklered.
(8) Combustiblepiping for central vacuum cleaning systems is permitted to penetrate a fire separation, provided the installation conforms to the requirements that apply to combustible piping specified in Sentence (3).
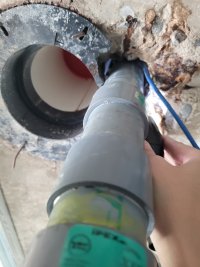
I found this in the code, but not sure if this is applicable to this situation:
3.1.9.4. Combustible Piping Penetrations
(1) Except as permitted by Sentences (3) to (8), combustiblepiping shall not be used if any part of the piping system penetrates,
(a) a fire separation required to have a fire-resistance rating, or
(b) a membrane that forms part of an assembly required to have a fire-resistance rating.
(2) Combustiblepiping that is part of a system described in Sentence (1) shall not be located in a vertical service space.
(3) Except as provided by Sentences (4) to (7), combustiblepiping is permitted to penetrate a fire separationrequired to have a fire-resistance rating or is permitted to penetrate a membrane that forms part of an assembly required to have a fire-resistance rating, provided the piping is sealed at the penetration by a fire stop that has an F rating not less than the fire-resistance ratingrequired for the fire separation when subjected to the fire test method in CAN/ulc-S115, "Fire Tests of Firestop Systems", with a pressure differential of 50 Pa between the exposed and unexposed sides, with the higher pressure on the exposed side.
(4) Except as required by Sentence (7), combustibledrain piping is permitted to penetrate a horizontal fire separation, provided it leads directly from a noncombustiblewater closet through a concrete floor slab and the piping is sealed at the penetration by a fire stop in conformance with Clause 3.1.9.1.(1)(a).
(5) Except as required by Sentence (7), combustiblepiping is permitted to penetrate a vertical or horizontal fire separation, provided the fire compartmentson each side of the fire separation are sprinklered and the piping is sealed at the penetration by a fire stop in conformance with Clause 3.1.9.1.(1)(a).
(6) Except as required by Sentence (7), combustiblepiping not more than 25 mm in diameter containing chlorine gas is permitted to penetrate a fire separation between a chlorine gas service room built in conjunction with a public pool or public spa and the remainder of the building, provided the piping is sealed at the penetration by a fire stop in conformance with Clause 3.1.9.1.(1)(a).
(7) Where combustible piping penetrates a firewall or a horizontal fire separation described in Sentence 3.2.1.2.(1), the piping shall be sealed at the penetration by a fire stop that has an FT rating not less than the fire-resistance ratingrequired for the firewall or horizontal fire separation when subjected to the fire test method in CAN/ulc-S115, "Fire Tests of Firestop Systems", and,
(a) the fire stopshall have been tested with a pressure differential of 50 Pa between the exposed and unexposed sides, with the higher pressure on the exposed side, or
(b) the fire compartments on each side of the firewall or horizontal fire separation shall be sprinklered.
(8) Combustiblepiping for central vacuum cleaning systems is permitted to penetrate a fire separation, provided the installation conforms to the requirements that apply to combustible piping specified in Sentence (3).
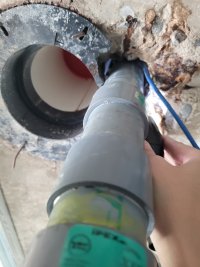