jar546
CBO
Are we there for this when a complaint comes in about a contractor?
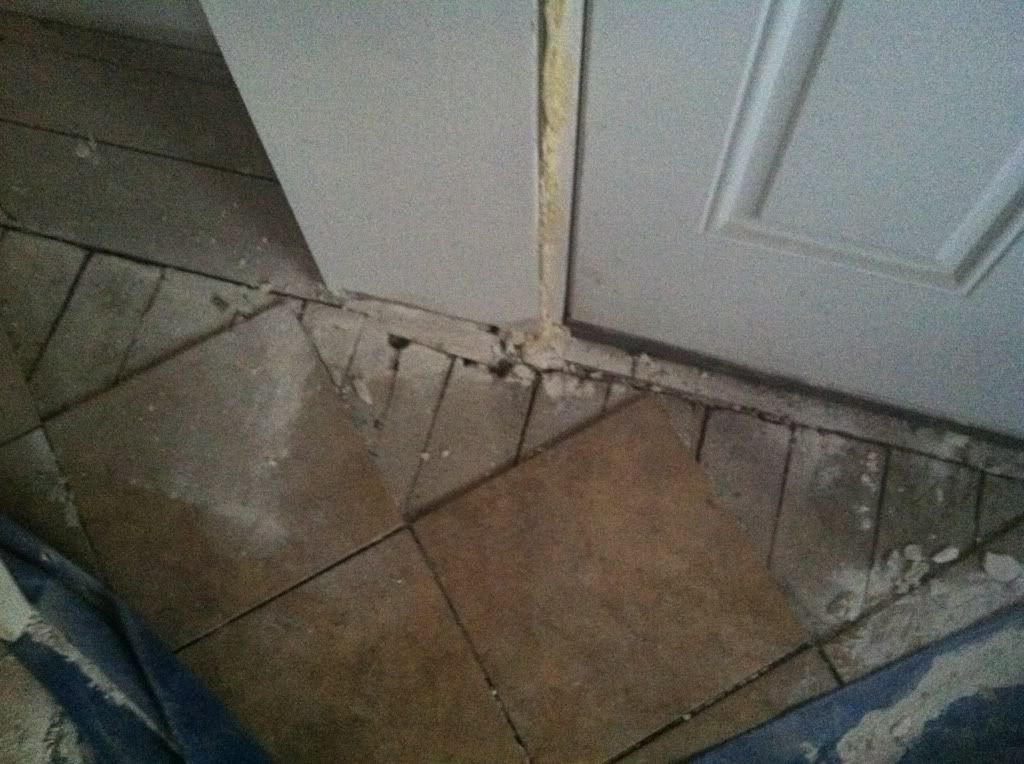
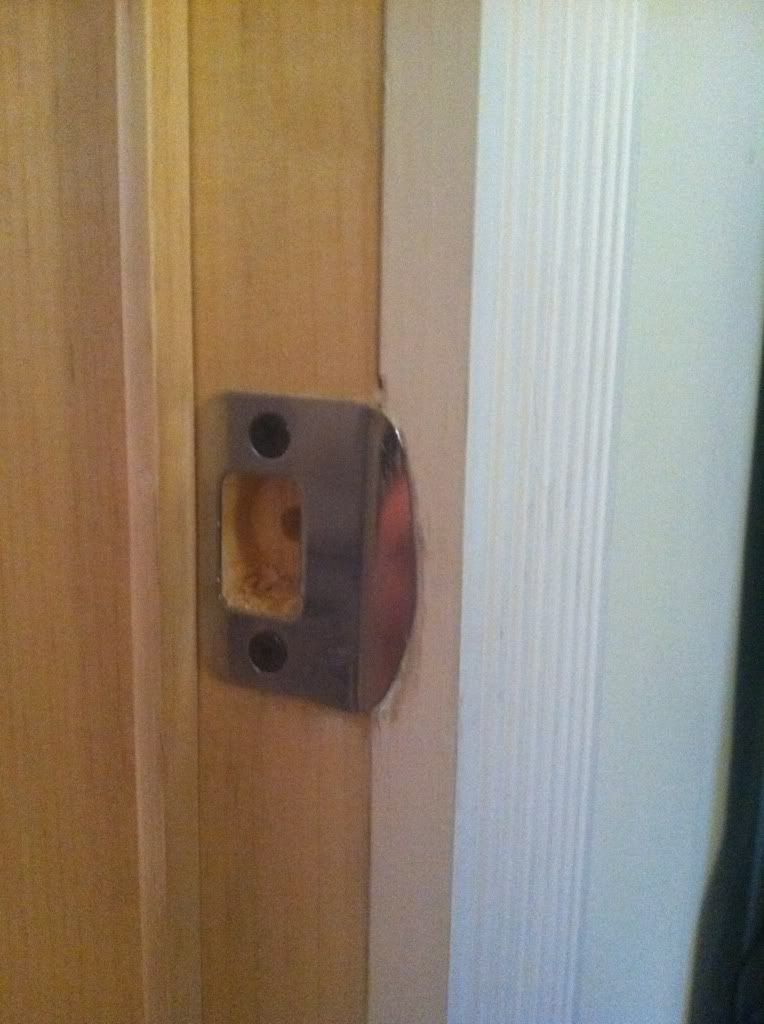
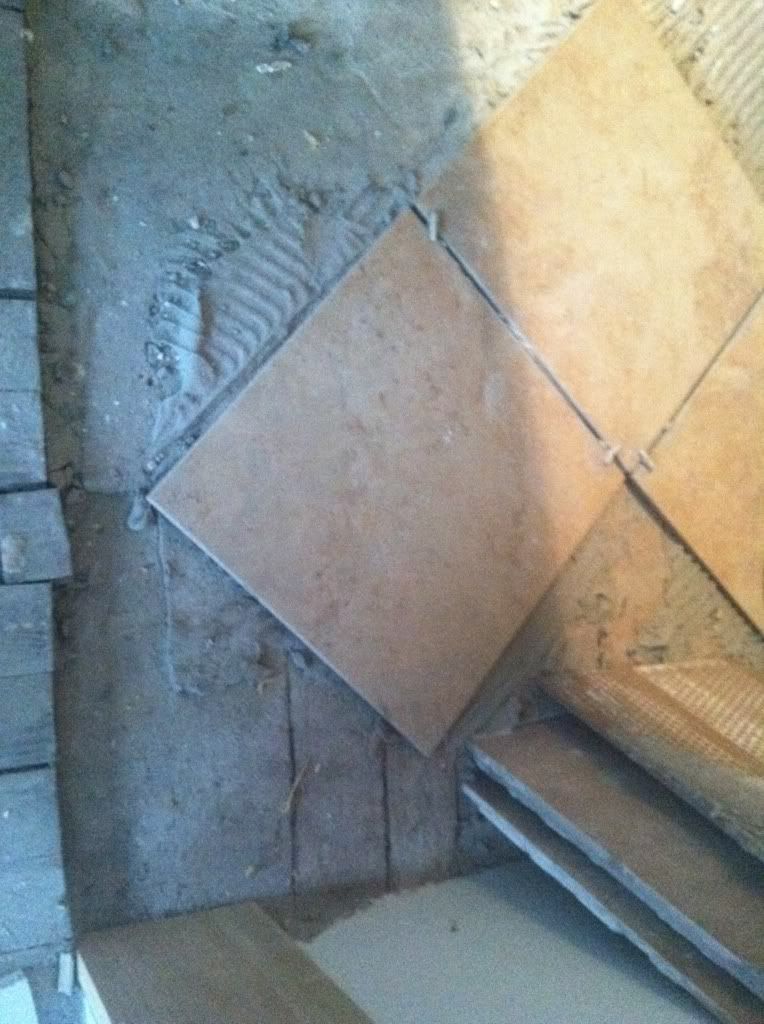
Your premier resource for building code knowledge.
This forum remains free to the public thanks to the generous support of our Sawhorse Members and Corporate Sponsors. Their contributions help keep this community thriving and accessible.
Want enhanced access to expert discussions and exclusive features? Learn more about the benefits here.
Ready to upgrade? Log in and upgrade now.
I just don't see us doing it at all. Of course we can per the NEC..........brudgers said:Once you start fooling with workmanship issues, what are you going to do with homeowner DIY projects?
I agree with this 100%. We used to like to "show off" to owners, inspectors, architects and engineers how good we were (or thought we were) Heck, alot of inspections were "formality walk-throughs" because the inspectors knew who the guys were trying to do it right. But at the same time, I think some of the inspectors were much better back in the day.Sandman said:I have been struggling with this issue for several years now and I have yet to understand why. I am not that old but when I was learning the trade it was seen as an insult, something to be embarrassed by, if an inspector or QC person found some fault with the work. The objective back then was to produce something to be proud of. We wrote our names on the framing before covering it up, “Built with Pride by __________ March 1992.”Now it seems the goal is to cut every corner and try to fool the inspector or QC person. I find that I have to be more of an investigator now. I must thoroughly check all the inspection reports, mill certificates, delivery tickets and interview people just to establish if some minor requirement was followed. Rarely am I told the truth until the evidence proves otherwise and then somehow I am made out to be the bad guy for discovering the failure. And the sad part is that nothing is really gained by cutting the corner; no time was gained and no money was saved but more importantly someone’s integrity and character were compromised in this futile exercise.
I do not see poor workmanship much in higher end residential or commercial work. Those projects seem to attract and keep a higher caliber workforce and management team. However, this is painfully common in production work, and unfortunately in government work where there is inadequate oversight. Poor workmanship will continue unabated until the client steps in and starts rejecting and not paying for the work.