chris kennedy
ADMIN
I had a GC here today to have some questionable fascia board replaced. He pulled down one 16' board and some soffit. Fascia is 2×6 and soffit material is ¼" plywood. He found that the ends of most of my trusses were either rotten or had inactive termite damage, therefore nothing to attach new fascia to without scabbing. I'm undertaking the project to renew my HO ins. He will patch this up to satisfy my ins co, but doesn't want to proceed further until I replace my roof. (note rotten T&G) He also mentioned that there should be another board between the trusses and fascia.
So I would like advice on what to expect when the inspector sees the truss situation? Also, in the second pic you see the roof vent, just vinyl screen attached with some kind of trim molding. What product would to recommend this gets replaced with.
Thanks for your time,
This is giving me a wicked walletache.
So I would like advice on what to expect when the inspector sees the truss situation? Also, in the second pic you see the roof vent, just vinyl screen attached with some kind of trim molding. What product would to recommend this gets replaced with.
Thanks for your time,
This is giving me a wicked walletache.
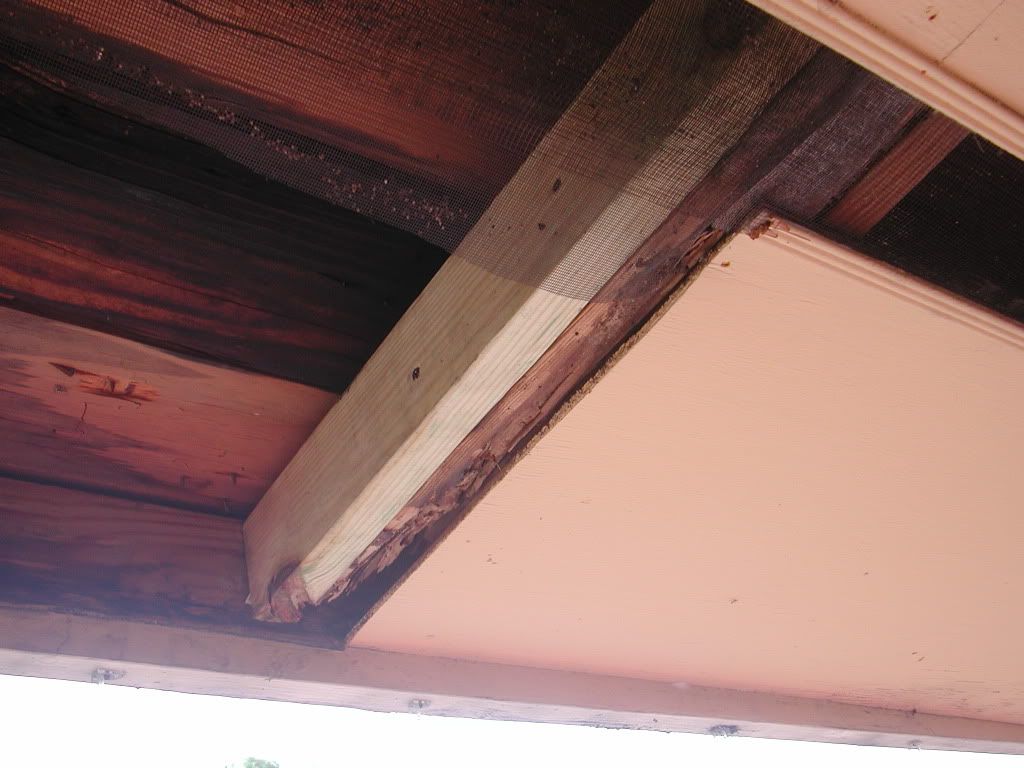
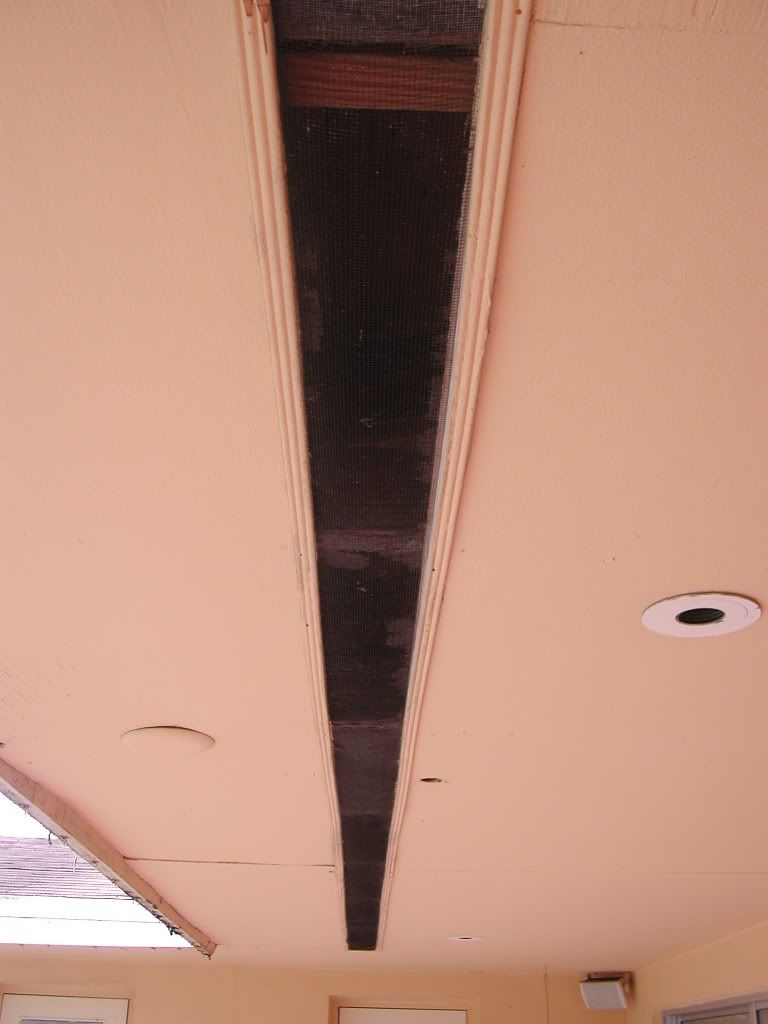