ICE
Oh Well
But should it be? Have you found violations with UL listed equipment?
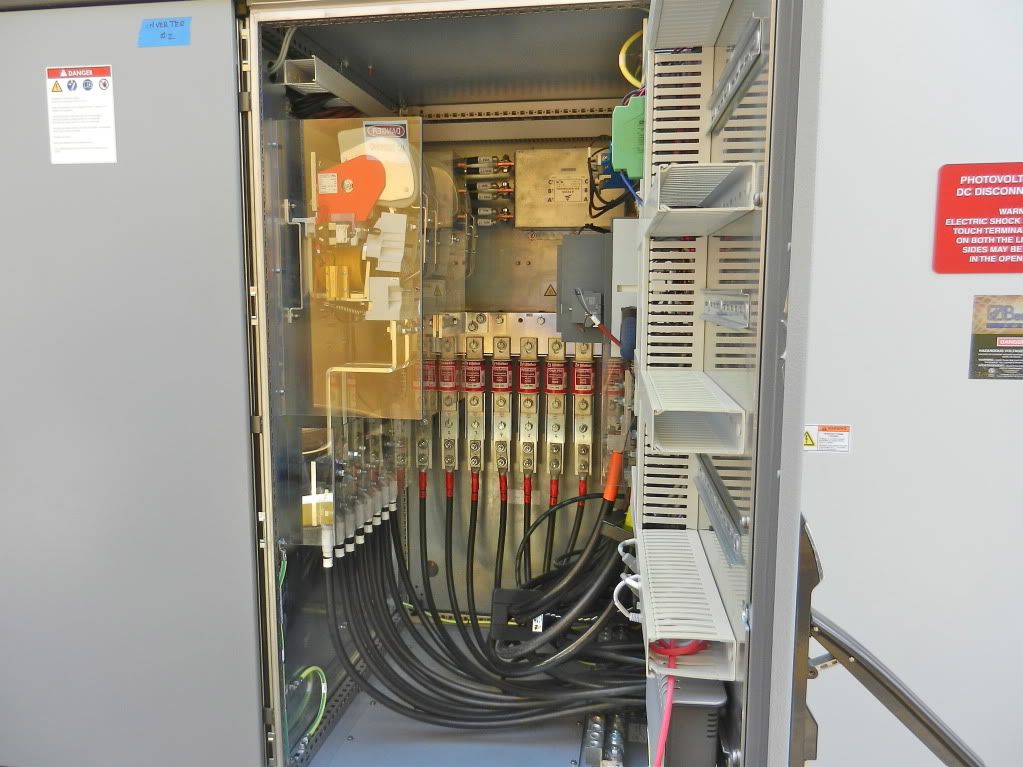
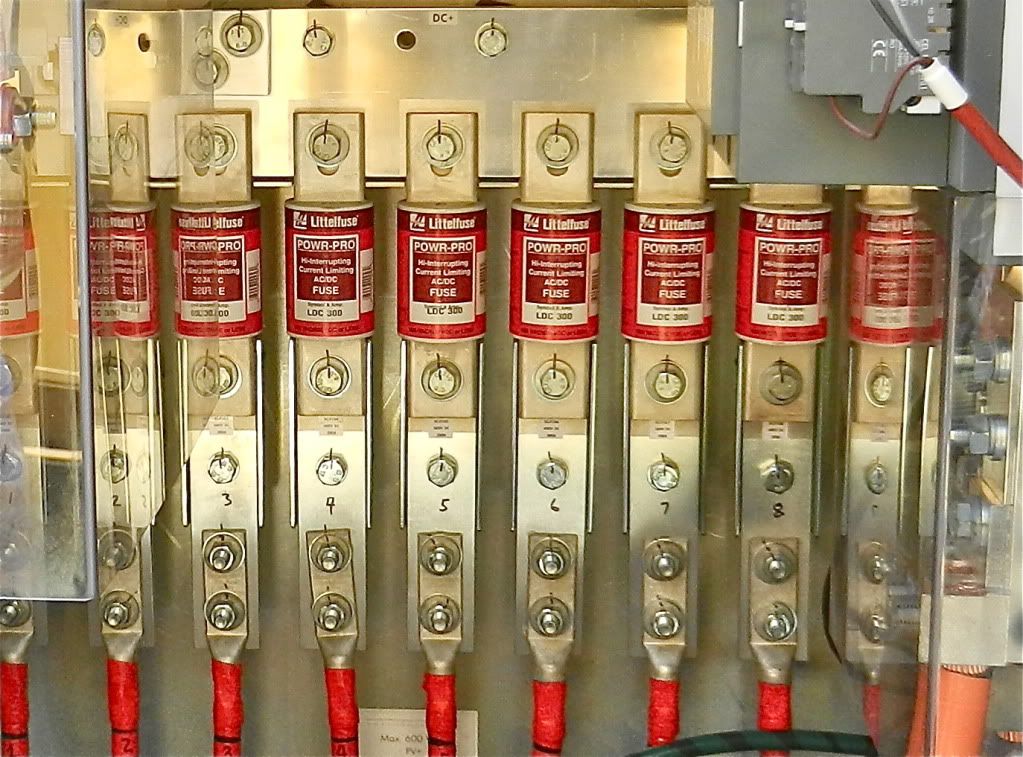
Last edited by a moderator:
There is no working space. To even get to several of the fuses, part of the shielding must be removed. This job is located in a city near where I work and the chief el. engineer invited me along. The lack of working space was caught by him on an earlier inspection. The job is a huge solar system that I mentioned in another thread.chris kennedy said:What problem are you addressing here. Wire size on the 300A fuses?
Sure I do, I'm the inspector and I found a code violation. UL is not infallible and I have caused UL to revoke a listing several times.Mark K said:If the code says the equipment must be listed amd it was properly listed then you do not have the authority to impose additional criteria related to vibration and possible chafing
I have done inspections where I would have sworn the contractor was trying to get me Pee'd off. I treated him the same way I would have treated the best contractor anyone could hope for. Being mad for any reason is no reason to change how you perform your job.tmurray said:I never understand contracts who will argue over installing something that costs a couple of bucks. Any contractor who wants to stay in business will quickly see that it is easier to spend a couple of bucks and keep the inspector happy than to **** them off. Personally I would recommend protecting the wires if there is no code violation and note that you recommended it. Later if there is a problem because the threads ate through the wires you can easily cover yourself and prove the contractor's negligence.
Did anyone read the units install instructions? My guess is that the manufacture intended for an installer supplied fitting to be used in those Meyers hubs. IMO the install pictured is in violation of 110.3. Also IMO Tiger has the option of 110.2 to disapprove the install.ICE said:The contractor is arguing that since the equipment is UL listed with this fitting for the conductors to enter the cabinet, I can't require an insulated or smooth bushing. My feeling is that the unit will vibrate and the conductors are against the threads which could cut through the insulation.![]()
Bravo! Such an insightful post showing the personality behind the keyboard is rare.jwelectric said:How was that for my first post?
Oh my goodness.gbhammer said:Eeny, meeny, miny moe,Catch a tiger by the toe.
If he hollers make him pay,
Fifty dollars every day