Ryan Schultz
SAWHORSE
Hi, I'm trying to get a grasp of the area and separation limitations of light-transmitting plastics.
The R-2 building is a 3 story, Type VB with a 20,000sf footprint, and is fully sprinklered.
Per 2607.4 Area Limitation and Separation exception 1:
... it appears this building would not be limited by 2607.4, but section 1406 instead.
All the exterior walls are 10ft or more away from a property line, or right of way.
We are proposing 2x wood stud construction behind the light-transmitting plastic panel (polycarbonate panel ) at each seam in the panel. The clip for the polycarbonate will be attached to the stud for lateral support.
These studs will be exposed to the interior space. That is, no concealed space.
There will be a horizontal alum profile supporting the top and bottom of the plastic panel at each floor.
---
Question: From what I can understand of Section 1406, assuming the incident radiant heat flux of these panel is less than 8.9(kW/m2), we are not limited in the maximum area, or the vertical separation of these polycarbonate panels. Since there is not a concealed space behind the panel, there is not a fire blocking requirement either.
Would this be a correct interpretation?
---
Also a related question, are these polycarbonate wall panels, with supporting studs behind, considered an 'opening protective'?
That is, would they fall under the restrictions of 705.8 Openings in exterior walls?
My interpretation is that they are not considered 'opening protectives'
---
If curious, this is the product we're looking to use: http://gallinausa.com/arcoplus/arcoplus-547/
Images below of the proposed design.
The R-2 building is a 3 story, Type VB with a 20,000sf footprint, and is fully sprinklered.
Per 2607.4 Area Limitation and Separation exception 1:
2. Veneers of approved weather-resistant light-transmitting plastics used as exterior siding in buildings of Type V construction in compliance with Section 1406.
... it appears this building would not be limited by 2607.4, but section 1406 instead.
All the exterior walls are 10ft or more away from a property line, or right of way.
We are proposing 2x wood stud construction behind the light-transmitting plastic panel (polycarbonate panel ) at each seam in the panel. The clip for the polycarbonate will be attached to the stud for lateral support.
These studs will be exposed to the interior space. That is, no concealed space.
There will be a horizontal alum profile supporting the top and bottom of the plastic panel at each floor.
---
Question: From what I can understand of Section 1406, assuming the incident radiant heat flux of these panel is less than 8.9(kW/m2), we are not limited in the maximum area, or the vertical separation of these polycarbonate panels. Since there is not a concealed space behind the panel, there is not a fire blocking requirement either.
Would this be a correct interpretation?
---
Also a related question, are these polycarbonate wall panels, with supporting studs behind, considered an 'opening protective'?
That is, would they fall under the restrictions of 705.8 Openings in exterior walls?
My interpretation is that they are not considered 'opening protectives'
---
If curious, this is the product we're looking to use: http://gallinausa.com/arcoplus/arcoplus-547/
Images below of the proposed design.
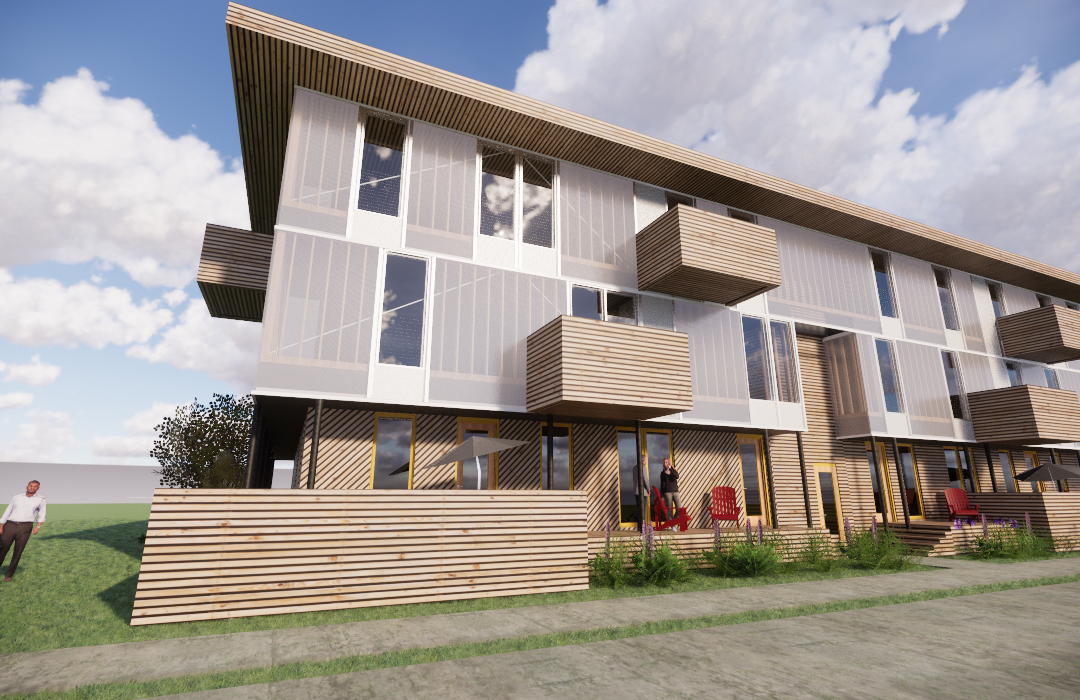
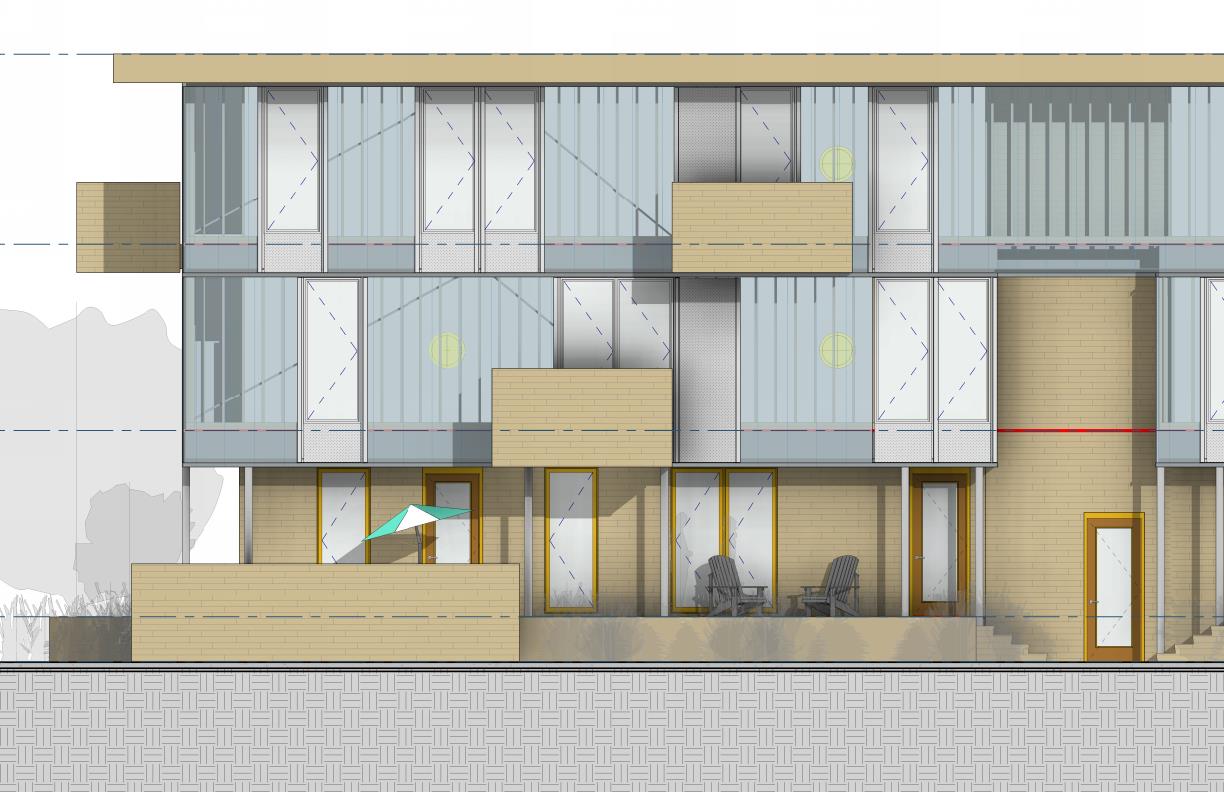