jar546
CBO
In many areas permits are not required for replacement windows unless they involve an egress window and sometimes, not even for that. I never liked the fact that in some towns we did not do replacement window inspections because I found so many of them installed improperly, especially when it came time for window flashing and energy code but hey, it is what it is and I guess it is buyer beware.
Then I moved to south Florida about 7 years ago and that all changed. I am now in a different world where you absolutely, positively require a permit and often 2 inspections, an in progress or "buck" inspection and a final. Due to the high wind zone we are in, 170mph+, and high positive and negative pressures, windows have to meet a lot of requirements and require an NOA or Notice of Approval by the state of Florida. Each manufacturer and each window must come with an NOA. The NOA gives you different methods of attachment and is an absolute must in order to perform your inspection because every window type had different anchoring requirements.
It starts with plan review which has to verify the wind zone and exposure category along with mean roof height, the height of the window to get the minimum pressures then matching up the NOA's to the window and location and verifying the window's design pressures meet or exceed the calculated wind pressures. The NOA has to be current and be approved for the current code cycle. Once this information is verified, a permit can be issued and a copy of the NOAs must be kept on the jobsite. On to inspections.
Some municipalities require buck inspections to make sure that the buck was properly installed and to verify which method of attachment the contractor will use as there are sometimes several or at least 2 options. Many municipalities just require that the contractor take photos during the change out and provide photos and an affidavit for the final inspection. For final, the attachment screws need to be verified and match the NOA and the window sticker must be kept on until the final inspection is over, otherwise it is difficult to match up and verify the NOA. The NOA is used to verify compliance with the screw pattern, size and depth included. The contractor will have to back out a few screws to verify they are using the right ones. Here are some photos from NOAs that need to be on the jobsite for all inspections. This process and inspections are taken very seriously here. I am just giving the basics and this is not an all encompassing post, just the basics.
It is not uncommon to have an engineer's stamp with drawings and charts for a replacement window/door job, especially in commercial buildings and mid or high-rise condos.
What does your area do about replacement windows?
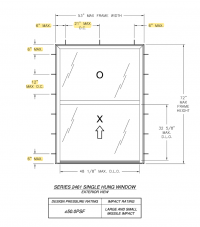
Then I moved to south Florida about 7 years ago and that all changed. I am now in a different world where you absolutely, positively require a permit and often 2 inspections, an in progress or "buck" inspection and a final. Due to the high wind zone we are in, 170mph+, and high positive and negative pressures, windows have to meet a lot of requirements and require an NOA or Notice of Approval by the state of Florida. Each manufacturer and each window must come with an NOA. The NOA gives you different methods of attachment and is an absolute must in order to perform your inspection because every window type had different anchoring requirements.
It starts with plan review which has to verify the wind zone and exposure category along with mean roof height, the height of the window to get the minimum pressures then matching up the NOA's to the window and location and verifying the window's design pressures meet or exceed the calculated wind pressures. The NOA has to be current and be approved for the current code cycle. Once this information is verified, a permit can be issued and a copy of the NOAs must be kept on the jobsite. On to inspections.
Some municipalities require buck inspections to make sure that the buck was properly installed and to verify which method of attachment the contractor will use as there are sometimes several or at least 2 options. Many municipalities just require that the contractor take photos during the change out and provide photos and an affidavit for the final inspection. For final, the attachment screws need to be verified and match the NOA and the window sticker must be kept on until the final inspection is over, otherwise it is difficult to match up and verify the NOA. The NOA is used to verify compliance with the screw pattern, size and depth included. The contractor will have to back out a few screws to verify they are using the right ones. Here are some photos from NOAs that need to be on the jobsite for all inspections. This process and inspections are taken very seriously here. I am just giving the basics and this is not an all encompassing post, just the basics.
It is not uncommon to have an engineer's stamp with drawings and charts for a replacement window/door job, especially in commercial buildings and mid or high-rise condos.
What does your area do about replacement windows?
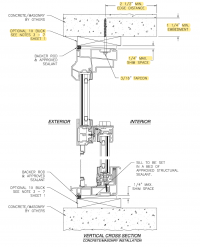
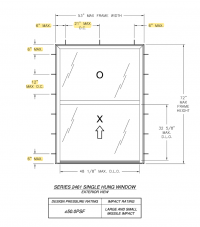